Table of Content
For example, they are sitebuilt homes in a factory setting under controlled conditions. There are fewer delays due to weather, availability of trades and late delivery of materials. Modular homes are cheaper to build, though this cost reduction is rarely the result of lowering their quality standards. Despite being prefabricated, modular homes are always built as permanent constructions and as such, they have to adhere to the local building codes. Usually, they assemble modular buildings in a factory-like setting under controlled conditions. Stick built homes are built onsite where builders have to deal with weather conditions that may delay completion.
On the downside, there are a few drawbacks to purchasing stick-built homes that buyers should know. Housing innovator Module is making progress on the first of a block of new houses in the Pittsburgh neighborhood of Garfield. It’s an exciting step forward for revitalizing the neighborhood with homes that are easy to construct and modify, energy efficient, and attractive. Sales tax costs – most states charge a sales tax of 50-65% of the total cost of the modular home.
What is the average cost to build a prefab home?
Factory builds typically benefit from all necessary third-party checks being performed as an integral part of the design and assembly process. This removes another common stall point for location builds, where inspections are carried out in situ, and problems flagged as they arise. Whether a particular project ends up being cheaper than traditional building depends on specific home designs and the cost of materials, plus the points mentioned above. If you’re still not sure which type of home is best for you, get connected with a local real estate agent. Local agents will explain the types of homes available in your price range to help you find the home that’s right for you, whether modular or stick-built.
They’re more energy-efficient and have lower monthly expenses than stick-built homes. Property deals often appear inherently more vulnerable to sources of potential legal dispute than many other investment projects. If mishandled, these may prove costly in terms of missed opportunities, loss of revenue, or even damage to individual and company reputation. We offer extensive, in-depth experience covering all aspects of commercial and private property litigation, as well as agricultural, greenbelt and brownfield contract law.
Getting your house in order – Top tips for seamless share-sale energy deals
The Connection Series is the higher-end line, with prices starting at $500 per square foot. Deltec is an option worth considering if you’re looking for an eco-friendly and sustainable prefab home. Exterior finishes – This includes the cost of siding, roofing, decks, porches, and other exterior finishes. The factories are located in the parts of the country with the lowest cost of manpower. The design that best represents the interests and passions of the customer is preferred over others.
Modular homes are transported to the site in sections and are NOT dependent on I- beams, which are typically removed after delivery. Floor joists with and, they support the units permanently and cannot be removed. Homes built from higher quality materials, regardless of if modular or stick-built, will have more worth. Stick-built homes have always had full customization from the beginning.
Material Costs
In the past, one of the major downsides to a modular home was the design and outside appearance. Unfortunately, traditional home construction tends to take longer than planned. One might need to move from their current home by a specific time. The home comes to the property with the wiring, insulation, doors, windows, plumbing, and flooring complete. One advantage lets you go to the site and see how it’s progressing.
There are many different types of manufactured homes available, from frame log cabins to modular homes and mobile homes. Firstly, prefab homes have to be constructed to meet strict building code regulations, supported by regular on-site inspections at every stage. This is more stringent than site-built homes which only require a single inspection. Another reason prefab homes are a safe option is due to the manufacturing process. Many people perceive modular homes as less desirable and lower quality than stick built homes.
What is the best foundation for a manufactured home?
Manufactured homes are typically eligible for financing through traditional mortgage programs or manufactured home loans. When looking for manufactured home builders, it is recommended to obtain quotes from several different builders to compare cost and quality. Manufactured homes can be purchased from manufactured home dealers, manufactured home retailers, or manufactured home builders. In general, manufactured homes are either built in a factory or shipped to their final destination in ready-to-assemble pieces. Manufactured homes have gained popularity in recent years as more people are looking for affordable housing options. Manufactured homes, which include A-frame log cabins, are popular choices for those looking to build their own home quickly and affordably.
The average cost of a modular duplex is $100 to $200 per square foot for a complete turn-key installation, depending on the size and customizations required. An average 2,000-square foot duplex costs $200,000 to $350,000 total after site prep, assembly, and finishing. Ft. modular home is $75,000 to $150,000 or $50 to $100 per square foot for a base model, not including customizations, assembly, or on-site finishing work. For the same house, expect to pay $120,000 to $240,000 total for a complete turn-key installation.
Getting a mortgage for a modular home is no different than any other house. On the other hand, if you want something uniquely yours, something customized, or a property that will impress the neighborhood, a modular home may not be the right fit. You might also try modular home sales near me to do a little research on your own before consulting with an agent.
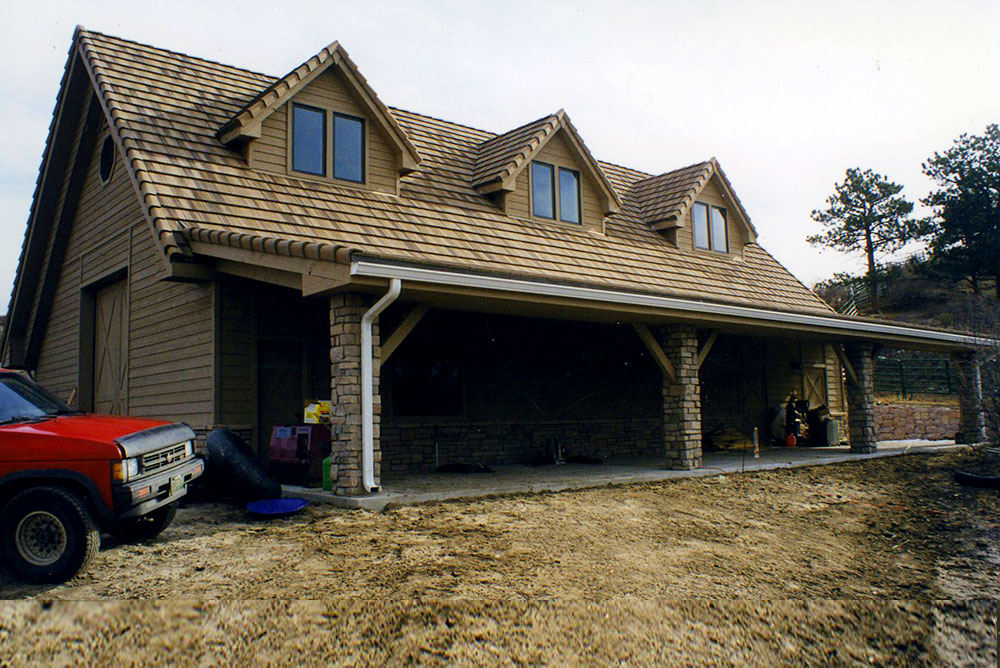
Two main types of residential housing include both modular and stick-built homes. These home types are often debated by buyers who want to be sure they’re making the best decision. Since there are many benefits and drawbacks of each type of home, you should carefully consider each before making a commitment. There are many differences between modular and stick-built homes.
Traditional house building methods have long had elements of prefab to them, with components like timber roof trusses being made off site. As home construction labor and material costs continue to rise – and those costs are reflected in new home prices – affordable options in many markets can be slim pickings. Today, modular homes have become more popular and match stick-built homes with quality materials.

The homes are built stronger to travel over the highways and be placed with a crane. The strength comes from extra materials and fasteners resulting in energy savings as a consequence. Your projects design is done by Mod-Tech Homes and production drawings and building engineering is done at our factories. The architecture and engineering costs (A&E) are reduced to your on-site needs only.
Are manufactured homes cheaper to build?
Bill Gassett is a nationally recognized Real Estate leader who has been helping people move in and out of the Metrowest Massachusetts area for the past thirty-six plus years. He has been one of the top RE/MAX Realtors in New England for the past two decades. What you need to know when buying a new home – find helpful advice on things to consider when you are purchasing new construction. There are some anecdotal claims they may even hold up better in storms than regular housing.

No comments:
Post a Comment